The Fundamental Solution
All non-intercooled superchargers
operate with an intake manifold temperature in the general range
of 115° - 200° above ambient (outside air) temperature at 8 psi.
At the same boost level, an Intercooled ProCharger operates
at only 28° above ambient! This tremendous advantage from cooler
air is just like the difference between driving your car on
a cold winter's day vs the blistering heat of summer! Thats
a real advantage that yields real performance. It
helps to understand that no supercharger alone will ever begin
to match the system efficiency of an intercooled supercharger
system. This is simply because compressing air creates heat,
as dictated by the laws of physics (Boyle's Gas Law). Even in
the case of "perfect compression" (100% adiabatic efficiency,
which is physically impossible without an intercooler - see
chart), air temperature would increase by approximately 71°
at only 8 psi, while the lower (40-80%) efficiencies of all
non-intercooled superchargers produce substantially higher temperatures.
Intercooled ProCharger systems are the fundamental, OEM solution
- because not only is less heat created when the air is compressed,
the majority of this heat is actually removed through intercooling.
The bottom line is that intercooled boost is substantially more
powerful and safe for your engine than hot, non-intercooled
boost. Now that technology has developed to the point that gear-driven
superchargers are powerful enough to reliably blow through an
intercooler, it simply doesn't make sense not to intercool,
especially for fuel injected applications running pump gas.
In fact, for high compression engines or continuous duty applications,
such as marine or towing, intercooling is absolutely essential
for reliability.
In basic terms, compressing air creates heat, while intercooling
removes heat. The illustration above may help to further
explain the tremendous impact of intercooling upon supercharger
system efficiency and engine intake temperatures:
Benefits
of Intercooling
- Greatly Reduced Intake Temperature
An 85° - 200° drop in air temperature (dependent upon
application) results in a more dense, powerful fuel/air
charge, greatly reduces exposure to detonation, and virtually
eliminates the "power fade" felt in back-to-back runs and
extended pulls without intercooling
- Full Timing
This reduction in temperature allows you to run factory
(or close to factory) timing, and avoids the substantial
horsepower loss inflicted by excessively retarded ignition
timing
- More Low-End Boost and Horsepower
The intercooler also acts as a passive wastegate, flattening
the boost curve at higher rpm's and allowing more boost
to be dialed in at lower rpm's
- An Expanded Power Band
Full timing and forced induction keep the engine pulling
hard to the redline
- More Boost
Not only will you experience the above benefits at any boost
level, you can also safely run substantially more boost
when intercooled!
Reliable
High Performance
Clearly, the only type of performance that matters is reliable
performance, and detonation is the single biggest threat to
engine reliability. The boost range for reliable performance,
without detonation, can be determined by looking at the type
of supercharger technology being considered, and the compression
ratio of the motor. With a lower compression ratio, an engine
can safely handle more boost, everything else being equal. Similarly,
if the temperature of the compressed air is lower, an engine
will have a much higher detonation threshold (the point at which
fuel ignites without a spark), and will be able to safely handle
more boost. The chart below helps to illustrate how the overall
efficiency of the entire supercharger system can be increased
by both leading edge supercharger efficiency and the use of
intercooling. Simply locate an engine's compression ratio at
the bottom of the chart and trace upwards to determine the maximum
reliable boost level. The amount of heat produced (adiabatic
effiency) by each supercharging technology is what determines
the boost limitation. While gear-driven centrifugal is clearly
the superior supercharger technology, it is also clear that
the biggest benefit comes from intercooling. These calculations
assume moderate timing, 92 octane pump gas, and a good supply
of fuel to the cylinders. As mentioned previously, detonation
is the single biggest threat to engine reliability. It is heat
and detonation that cause blown head gaskets and burned pistons,
not boost. Achieving maximum performance from a given
engine while avoiding detonation requires the right combination
of intake air temperature, timing and fuel quality. For example,
without intercooling a stock 5.0 with 9.5:1 compression ratio
can only hold 5-6 psi of boost before detonation becomes a problem.
The only way to safely run more than 6 psi of boost and still
make a meaningful increase in power without an intercooler is
by using racing fuel to avoid detonation.
Many companies also employ "band-aids" such as ignition retard
and larger injectors to run 8-9 psi on pump gas, but the resulting
increase in performance is only marginal (since both of these
band-aids suboptimize) and detonation is frequently still a
problem.
Detonation
We've all heard of this, but what is it? Detonation, or
engine knock, occurs simply when fuel pre-ignites before the
piston reaches scheduled spark ignition. This means that a powerful
explosion is trying to expand a cylinder chamber that is shrinking
in size, attempting to reverse the direction of the piston and
the engine. When detonation occurs, the internal pneumatic forces
can actually exceed 10x the normal forces acting upon a properly
operating high performance engine. Detonation is generally caused
by excessive heat, excessive cylinder pressure, improper ignition
timing, inadequate fuel octane or a combination of these. Of
the previous, excessive heat is usually the culprit. As an engine
is modified to generate more power, additional heat is produced.
Today's pump gas will only tolerate a finite amount of heat
before it pre-ignites and causes detonation.
Although forced induction engines usually produce far less heat
than comparable naturally aspirated high compression engines,
the cylinder temperatures in intercooled engines are radically
cooler yet. It is rarely boost that causes detonation, just
unnecessary heat. An intercooler is such a natural solution
for forced induction, that in almost every OEM application,
intercooling is part of the package.
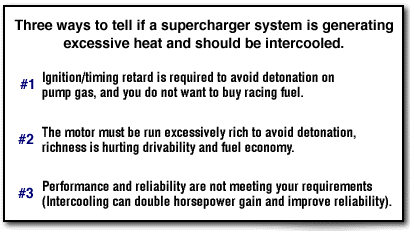
Air vs Water
Accessible Technologies manufactures both air-to-air and air-to-water
intercooler systems, and the guidelines for their usage are
fairly straightforward.
For automotive street applications, air-to-air technology is
easy to install, highly effective, extremely reliable since
it has no moving parts, and requires no maintenance. Air-to-water
intercooler systems, on the other hand, are much more difficult
to install as they contain an intercooler, a separate radiator
to cool the water, a water tank, and a pump. But probably the
biggest drawback to air-to-water on the street is that this
technology requires the addition of ice to match the efficiency
of air-to-air technology. Additionally, the requirement of ice
and the possibility of pump failure or leakage means that air-to-water
is also inherently less reliable.
For race-only applications, air-to-water works well since the
need to add ice at the track prior to each run is not a big
drawback. The other issues are the same as listed above for
street applications, and efficiency will be comparable with
the use of ice.
For marine applications, air-to-water is the preferred technology,
for three primary reasons. First, the installation of a pump
and radiator are no longer required (the lake or ocean is the
radiator, and boats already have a water pickup/pump). Second,
ice is not required, given the availability of massive amounts
of cool lake or ocean water into which heat can be transferred.
And finally, since boat engines are typically situated in the
rear rather than in the front (like most automobiles), it would
be very difficult to find adequate airflow for an air-to-air
intercooler in the back of the boat. |